Cu/Al复合板渐进成形过程力测控系统设计及成形质量控制毕业论文
2021-11-30 23:20:27
论文总字数:15332字
摘 要
与单金属板材相比,金属复合板材越来越受到人们的关注,因为它能够将不同性能材料的优点结合在一起,如高强度、低密度和良好的耐蚀性。然而,金属复合板材在渐进变形时的变形行为却不同于单金属板材,在这方面,我们可以通过建模分析、经验公式的方法,并且进行改变工艺参数的实验,对铜铝复合材料的渐进变形行为进行了全面研究。结果表明,在工艺参数改变的情况下,金属复合板材的成形性、表面粗糙度、厚度变化和成形力均与单层板材不同。
本文我主要从四个方面来进行课题的研究,首先是研究工艺参数对于复合板成形性能和零件表面质量的影响;其次是对复合板成形过程有限元建模并进行实验验证;接着是对复合板单道次成形成形力的研究;最后是对复合板多道次成形力的研究。
关键词:铜铝复合板;渐进成形;成形力;成形质量;有限元
Abstract
Compared with single metal sheet, metal composite sheet has attracted more and more attention because it can combine the advantages of different properties materials, such as high strength, low density and good corrosion resistance. however, the deformation behavior of metal composite sheet is different from that of single metal sheet during progressive deformation. in this respect, we can comprehensively study the progressive deformation behavior of copper-aluminum composite by modeling analysis, empirical formula, and experiments to change process parameters. The results show that the forming ability, surface roughness, thickness variation and forming force of the metal composite sheet are the same as that of the single layer when the process parameters change Different plates.
In this paper, I mainly study the subject from four aspects, first is to study the influence of process parameters on the forming performance of composite plate and the surface quality of parts; second is to model the finite element of composite plate forming process and carry out experimental verification; then is to study the single-pass forming force of composite plate; finally, to study the multi-pass forming force of composite plate.
Key Words:Cu-Al composite sheet; Incremental sheet forming; Forming force;Forming quality; Finite element method.
目 录
第一章 绪论 1
1.1引言 1
1.2板料成形技术的发展 1
1.3 全文框架 2
第二章 铜铝复合板渐进成形的实验研究 3
2.1实验材料 3
2.2实验设备 3
2.3工艺参数对于成形性能的影响 4
2.3.1板料渐进成形性能评估 4
2.3.2轴向进给量对铜铝复合板渐进成形性能的影响 5
2.3.3进给速度对铜铝复合板渐进成形性能的影响 5
2.3.4工具头直径对铜铝复合板渐进成形性能的影响 7
2.4工艺参数对铜铝复合板渐进成形零件表面质量的影响 8
2.4.1板料数控渐进成形零件表面质量的分析 8
2.4.2轴向进给量对铜铝复合板渐进成形零件表面质量的影响 9
2.4.3成形角对铜铝复合板渐进成形零件表面质量的影响 10
2.4.4工具头直径对铜铝复合板渐进成形零件表面质量的影响 11
2.5铜铝复合板渐进成形零件的界面分析与壁厚分布 12
2.5.1铜铝复合板渐进成形零件的界面分析 12
2.5.2铜铝复合板渐进成形零件的壁厚分布 12
第三章铜铝复合板渐进成形有限元建模与实验验证 15
3.1有限元模拟软件介绍与使用 15
3.2有限元建模 15
3.2.1部件的建立与装配 15
3.2.2定义材料属性 15
3.2.3网格划分与算法选择 16
3.2.4接触和摩擦的定义 16
3.2.5边界条件与载荷的定义 16
3.2.6分析步与前处理的设置 17
3.2.7作业提交与后处理 17
3.3铜铝复合板渐进成形有限元模型的实验验证 18
第四章铜铝复合板单道次成形成形力的研究 21
4.1板料数控渐进成形力的理论分析 21
4.2板料数控渐进成形力的测量数据分析 21
4.3工艺参数对渐进成形成形力的影响 21
4.3.1轴向进给量对铜铝复合板渐进成形力的影响 21
4.3.2成形角对铜铝复合板渐进成形力的影响 23
4.3.3工具头直径对铜铝复合板渐进成形力的影响 24
4.3.4轴向成形力经验公式的校正 25
第五章 铜铝复合板的多道次成形 27
第六章 总结与展望 30
参考文献 31
致谢 32
第一章 绪论
1.1引言
双金属复合材料被广泛应用于复合材料的结构和构件中,在航空航天、电气、化工、船舶和建筑等行业有着广泛的应用,因为它利用了不同基材的机械、物理和化学性能相结合的优势。同时由于日益严重的能源危机,人们更加追求高性能高性价比的复合材料[1]。复合材料通过采用特殊的技术能够组合成为新型材料,能够弥补单种材料的性能缺陷[2]。传统的金属板料成形主要是通过冲压完成的,而冲压工艺必须使用模具,因此有着周期长、成本高的缺点,这也导致了它不能适应小规模生产、小批量生产的模式。近年来,各国也越来越多地关注双金属复合片的形成过程,比如日本有90万吨的产量,而韩国俄罗斯等国家也注重于研究复合材料[3]。
1.2板料成形技术的发展
Parsa等人[4]通过数值和实验研究了厚度比以及层布置对铝/不锈钢两层薄板深拉中可达拉伸比的影响。结果表明铝与钢的厚度比为1/3,可得到最大的拉伸。Bagherzadeh等人[5]建立了分析模型,对Al/碳钢片的水机械深拉进行应力分析和失稳条件。然后,根据所建立的模型,分析了层厚、布置、拉拔比和摩擦条件对成形过程的影响。结果表明,薄板的铺层和厚度可以改变工作压力区.在进一步的工作中,通过建立良好的FE模型,预测了铝/钢板成功成形的合适工艺条件。 Karajibani等人[6]通过数值和实验方法研究了Al- Steel薄板在深拉过程中的成形性,结果表明通过改善板层厚度、模具圆弧半径和毛坯与凸模之间的摩擦,可以提高两层金属薄板的拉伸比。由 Dehghani和Salimi进行了分析和实验分析,研究了铜不锈钢板在深拉深中的成形性。[7]据报道,较强层(不锈钢)的厚度变化比较弱层(铜)更均匀。此外,在不同的层排列中,从各种因素来看,双金属薄板的成形性与单层薄板具有相同的趋势。
随着对双金属材料定制部件的需求不断增加,有必要开发新的成形技术来处理双金属复合材料,而不是传统的深拉或冲压。单点增量成形(SPIF)作为一种新兴技术,在过去的十年中进行了深入的研究。在成形期间,局部到形被一个相对较小的工具叠加到一个薄片上,该工具遵循一个路径,直到达到一个最终的形状。这种独特的变形机制带来了主要的好处,如与传统的拉伸和冲压工艺相比,它有着更好的成形性、更低的成形力、不成形模具和所需的复杂设备,使其非常适合快速成型和低容量生产。Al Ghamdi等人[8]研究了铜铁复合材料片材SPIF过程中退火对粘结力和成形性的影响。结果表明,最合适的退火温度为700°℃。此外,没有观察到分层形成,直到达到最大角度。在参考文献中[9]还采用退火来减少硬化效应,然后进行了各种表征试验,包括冲压和SPIF工艺中的成形性。结果表明,随着退火温度的升高,冲压和SPIF的成形性都会增加。此外,还发现冲压中的分层限制了成形性,而在SPIF中却没有发现。利用数值和实验研究了铜铝两层薄板的SPIF.Honarpisheh等人[10]结果表明在所研究的双金属材料的增量成形过程中,随着刀具半径和台阶尺寸的增大,成形力增大,壁厚减小。Sakhtemanian等人[11]研究了低碳钢(St)和纯钛(Ti)双金属薄板层排列对成形工艺的影响。他们的结论是Ti-St的排列比St-Ti表现出更高的成形力,这是由于Ti-ST模式下Ti层的孪晶密度比St-Ti模式高两倍,从而导致了更多的加工硬化。
卢仁伟等人[12]对0Crl8Ni9不锈钢板料表面进行了不同的化学处理,结果表明经过草化处理的板材渐进成形后的表面形貌更好。这是因为板材表面生成了草酸盐润滑载体。沈长艳等人[13]在不同润滑条件及表面处理方法下渐进成形了 TA1板料,结果发现使用质量比4:1的二硫化铝与凡士林混合物作为润滑剂,同时在板料表面用微弧氧化工艺覆盖氧化膜能够有效改善零件表面质量。
王会廷等人[14]利用导热油开发了液体介质传热渐进温成形,以此来改善板料的渐进成形性能。为了扩大板料数控渐进成形技术的应用范围,张淑芹等人[15]研究了金属网孔板的渐进成形性能。
1.3 全文框架
图1.1全文框架
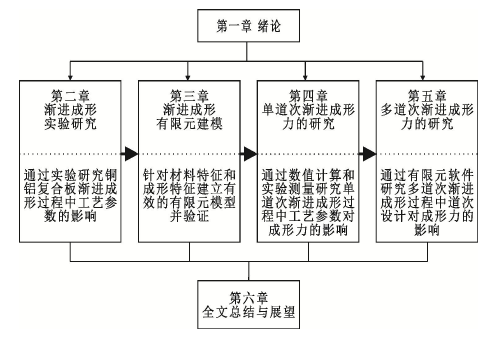
- 铜铝复合板渐进成形的实验研究
2.1实验材料
本研究采用洛阳铜一金属材料开发有限公司提供的铜(C10100) 和铝(Al1060-O)复合板材,总厚度为1mm。 铝Al1060-O和铜C10100片的原始厚度约为轧制前8.5毫米和1.5毫米。轧制后,铝和铜层的平均厚度为分别为0.85mm和0.15mm。此外,还提供了厚度为0.9mm和0.1mm的平均铝和铜层的双金属片以及厚度为1.0mm的单层铝-Al1060-O和铜-C10100片。 将Cu-Al复合材料切成尺寸为200mm×200mm的小块作为准备使用。为了评价Cu-Al复合材料片材的力学性能,最终我们在一台最大载荷为100kN的万能测试机(型号:DNS-100,由Sinotest设备有限公司制造)上,用狗骨状试样沿轧制、对角线和横向进行拉伸试验。
在拉伸试验中,应变速率设定为5mm/min。对于每个样本, 重复三次测试以获得平均值。拉伸性能在三个方向上的各向异性并不那么明显,因此在下面的建模中,它们将假定为各向同性, 铜、铝及其复合材料的力学性能列于图2.1中。
请支付后下载全文,论文总字数:15332字
相关图片展示: