第八代凯美瑞轿车制动器的轻量化设计毕业论文
2020-02-17 12:50:55
摘 要
本文目的是对第八代凯美瑞轿车的制动器进行轻量化设计,首先依据汽车设计及相关设计经验,确定了本次设计采用浮钳式盘式制动器,并完成制动管路的选择和真空助力装置的设计,然后利用凯美瑞轿车制动器的设计基础参数进行制动器主要结构参数设计,再利用CATIA软件进行三维模型建立,并完成二维图纸设计;本次设计第二部分是对设计的制动器进行轻量化设计,轻量化的方向选择材料C/C-SiC,通过数据分析显示其应用于制动器轻量化的优越性;最后一部分是运用abaqus软件对制动器制动过程进行数值模拟,通过分析制动盘制动过程的热应力特征变化和温度场特征变化,进而分析C/C-SiC复合材料应用于制动器轻量化的优越性和合理性,最后分析C/C-SiC复合材料的制动器的抗热衰退性能。
关键词:制动器,轻量化,abaqus,C/C-SiC
ABSTRACT
The purpose of this paper is to lightly design the brakes of the 8th generation Camry car. Firstly, based on the design of the car and related design experience, the design uses the floating clamp disc brakes, and completes the selection of the brake pipe and the vacuum booster. The design, then use the design basic parameters of the Camry car brake to design the main structural parameters of the brake, and then use the CATIA software to build the 3D model and complete the 2D drawing design; the second part of the design is to lightly design the brakes. The lightweight direction selection material C/C-SiC shows its superiority in brake weight reduction through data analysis. The last part is to use abaqus software to simulate the brake braking process and analyze the brake disc braking process. The thermal stress characteristic changes and temperature field characteristics change, and then the superiority and rationality of C/C-SiC composite materials applied to brake lightweighting are analyzed. Finally, the thermal decay resistance of C/C-SiC composite brakes is analyzed.
Key words:Brake; lightweight;abaqus;C/C-SiC
目录
摘要 I
ABSTRACT II
第一章 绪论 1
1.1制动器简介 1
1.2国内外汽车制动器轻量化发展现状与未来趋势 1
第二章 制动器总体设计和结构设计 4
2.1第八代凯美瑞制动器结构与工作原理 4
2.2制动器管路选择 5
2.3第八代凯美瑞制动器设计技术参数 6
2.4浮钳盘式制动器的主要参数选择及计算 6
2.4.1制动盘直径D 6
2.4.2制动盘厚度h 6
2.4.3摩擦衬块外半径R2与内半径R1 7
2.4.4摩擦衬块工作面积A 7
2.4.5 制动驱动机构对制动盘的压紧力F0 7
第三章 制动器和驱动机构设计及计算 8
3.1同步附着系数φ0 8
3.2制动器制动力分配系数 8
3.3前后轮制动力矩确定 8
3.4摩擦衬片的磨损特性计算 9
3.5制动轮缸直径d和工作容积V 10
3.6制动主缸直径d0 10
3.7制动踏板力Fp和制动踏板工作行程Sp 11
第四章 制动器轻量化和仿真分析 12
4.1 C/C-SiC应用于制动器轻量化合理性 12
4.2 制动器制动过程数值模拟 13
4.2.1 数值模拟前提条件 13
4.2.2 通风盘式制动器尺寸与材料参数 14
4.2.3 制动器制动仿真过程 15
4.2.4制动器制动过程数值模拟结果分析 17
4.2.5 热衰退性分析 20
第五章 结论 22
参考文献 23
附录 MATLAB编制制动力分配曲线 25
致谢 26
第一章 绪论
1.1制动器简介
制动器是汽车的制动系统的主要组成部分。制动系统的作用第一是减速运行的汽车停下来,也就是驱动制动;第二是保持汽车在长下坡状态稳定的速度和制动器的抗热衰退性的优异性能,即,辅助制动;第三是使停止的汽车,保持静止状态,即驻车制动[1]。目前,汽车制动系统的制动器主要使用摩擦制动器,摩擦制动器之一是鼓式制动器,鼓式制动器大多应用于商用车辆。另一种是盘式盘式制动器,它主要是用于乘用车。本次设计的是第八代凯美瑞轿车,属于乘用车。随着技术的进步,越来越多的新技术被应用到盘式制动器,例如液压助力和空气辅助盘式制动器。使盘式制动器的制动力更稳定,散热效果更好。它适用于各种路况,所以对汽车盘式制动器更广泛的应用。
盘式制动器进一步细分,一般根据摩擦副中的固定元件划分为全盘型和卡钳型。本次设计的第八代凯美瑞轿车的盘式制动器选择卡钳型,而卡钳型盘式制动器可分为浮动卡钳盘式制动器和固定卡钳盘式制动器。固定卡钳盘式制动器的缺点是制动钳固定不动,既不能旋转又不能移动,固定安装在轴上,使得制动钳的工艺结构制造难度加大,且要分布管路,使制动钳尺寸变大,安装不方便,这些缺点使其适应现代汽车的需求。浮动钳盘式制动器的卡钳可以沿轴向相对于该制动盘滑动,并且只需要被提供有一个单侧缸。因此,具有结构紧凑,安装方便的优点,所以大多数现代汽车选择浮动卡钳盘式制动器。
1.2国内外汽车制动器轻量化发展现状与未来趋势
汽车轻量化是现代汽车发展的趋势,轻量化概念应用于汽车结构的各个方面。如轻巧的车身,轻巧的底盘,轻巧的发动机等,优化的方向可以在结构上也有从材料上,可以对系统结构优化,也可以对零部件优化,其概括表现有:
(1)研究和应用轻质材料,如铝,钛,镁和其他合金,粉末冶金和合成塑料和陶瓷复合材料,并对材料的相关理化性质进行研究,且根据不同的轻量化零部件校核相关参数,保证质量。
(2)使用CAD,CAE等计算机辅助技术来构建和模块化汽车零部件。包括应用拓扑优化等理论分析汽车结构,确定优化部位,再利用计算机技术校核。
1)在结构上进行轻量化研究
对制动器进行结构上优化设计,从而达到轻量化的目标国内外学者运用多种方法产生大量的科学研究论文与成果。对楚正中,万连恩,丁慧慧的研究是基于有限元分析的方法,使用abaqus来对盘式制动器进行建模。根据安全系数云图和制动器壳体,卡钳体,卡钳体支架的复合应力云图分析气动盘式制动器,优化这三个主要部件的设计,实现轻量化;王宏斌,奚乐的研究利用了拓扑优化方法,确定了降本减重的关键零件,并辅助有限元分析软件,在确保性能的前提下,通过减少主要部件中使用的材料量,可以减轻制动器的负担;唐金元和赵国维的研究建立了ISIGHT的集成CATIA,ABAQUS和MATALAB优化工艺,用于轻量化设计计算,减少了卡钳的疲劳寿命,同时将质量减少了5%。它对整体制动器的轻量化设计具有参考意义;陈征皞研究使用UG,CAE,HYPERMESH和ABAQUS软件分析制动器在一定载荷和约束下产生的偏移,扭转和应力,并分析可轻微加工的零件。调整,缩小所有指标和目标值之间的差距,并成功实现减重,同时减少部分磨损的可能性。
2)在材料上的轻量化研究
从材料上进行轻量化一般是选取制动器的某一结构部件,其中制动盘和摩擦片的制动材料的选用对制动器的性能和轻量化起主要因素,因此如何选择和如何制备性能优良的适用于制动器的材料非常关键。制动器制动工作时所遇的工况较为复杂,因此研究在不同的工况下制动器选用新型制动材料后,制动盘与制动摩擦片的摩擦稳定性是国内外学者的研究和探索的一个重点。
崔星在研究中对采用了C / SiC复合材料的制动盘进行了机械试验,对其机械特性和C / SiC复合材料的热性能进行了研究。分析结果表明,该C / SiC复合材料的制动盘和摩擦对中的摩擦衬片之间的摩擦系数与制动压力的增加而略有下降。此外,他还研究了在潮湿条件下的刹车制动状态。此时,摩擦对之间的摩擦系数由小于传统铸铁制动盘的摩擦系数;李娜研究了FeSi75改性C / C-SiC制动材料,基于C / C-SiC复合材料提高了制动盘的耐磨性; XuXingya, FanShangwu等研究在干燥、淡水、海水和静态条件下制动,对摩擦副采用C/SiC-C/C对,对偶静摩擦系数( COF)较C/C-C/C的对偶静摩擦系数有较大提高,此外, C/ SiC- C/ C的稳定性几乎不受淡水和海水的影响,对于应用C/SiC-C/C, C/SiC的制动盘磨损量很小,这样可以使制动器使用的C/SiC盘更薄。在直径相同和数量一致的制动器的制动盘选择时,制动器使用C/ SiC-C /C对复合材料可以比使用C/SiC -C /SiC对复合材料,轻量化的效果更好;FanShangwu,ZhangLitong等研究采用化学气相渗透、浆体渗透和液态硅渗透三步法制备了具有夹层结构的C/SiC复合制动材料。所制备的制动材料包括一个富C纤维的主体和两个表面富硅的摩擦层。研究表明具有夹层结构的C纤维/SiC在潮湿状态下没有衰减,并且性能优于三维针刺碳纤维/碳化硅。夹层结构C / SiC的静摩擦系数和线性磨损率均高于三维针刺C / SiC;Chen Guanyi和Li Zhuan研究了C / C-SiC复合材料的摩擦磨损性能和制动过程中的热应力行为。模拟高速轨道制动条件下 C/ C- SiC复合材料的自双摩擦磨损试验, C/ C- SiC复合材料制动过程中表现出优异的静摩擦因数(0.68)以及动摩擦因数(平均值为0.36);W. Krenkel,F。Berndt等研究发现Si C(高)和Si 铸铁(高)材料的制动摩擦片的摩擦系数较大,摩擦系数对温度和环境的稳定性比较优异,此外与加硅和铜的摩擦片相比较,加硅和铜的摩擦片摩擦系数较小且对工况和环境的变化有较大变化。
第二章 制动器总体设计和结构设计
2.1第八代凯美瑞制动器结构与工作原理
查阅相关资料,可以发现第八代凯美瑞制动器使用的是浮动卡钳盘式制动器。由图可知第八代凯美瑞的制动系统的主要结构是由制动踏板和助力装置以及浮钳盘式制动器组成,其中助力装置采用真空助力装置和液压管路传递制动踏板力,浮钳盘式制动器的主要部件有制动钳壳体、制动钳活塞、制动钳支架、制动盘以及摩擦片组成[1]。
制动系统的工作原理是在汽车需要制动时,通过制动踏板移动相应的距离获得需要的制动效果,制动踏板产生的踏板力在经过真空助力器后将会放大相应的倍数,然后放大后的制动踏板力经过制动主缸变换成制动液压力。制动液压再经过管道传递,最后作用在制动钳壳体体内的活塞侧上,制动液压压动活塞压向制动摩擦片,在摩擦片上产生制动压力,制动液压对制动钳壳体的反作用力使制动钳壳体与活塞反向滑动,这样制动钳壳体将对另一侧的摩擦片产生制动压力,这样制动盘两侧的摩擦片将产生相等的制动压力,摩擦片与制动盘构成摩擦副,制动力产生制动力矩,使摩擦片与制动盘之间的旋转运动减速甚至趋于停止,而且制动器与车轮是固联安装,制动器与车轮旋转运动一致,从而可以完成制动的目标。

图2.1 浮钳盘式制动器工作原理
2.2制动器管路选择
综合考虑,本次设计建议使用液压制动器,这种制动器已被广泛认可用于汽车制动器。从安全性的角度来看,以确保汽车的制动性能的可靠性,应该有至少两个独立的制动线路。即是整体车辆的所有行车制动器,它们的液压或气动管路均需被分成两个或更多个独立回路[3]。
用于双轴车辆的双回路制动系统具有以下五种常见的分体式:单轴连接单轴(II)型(图a),十字(X)型(图b),单轴半到半轴(HI)型(图c),半轴单轴半轴单轮(LL)型(图d),双半轴双半轴(HH)型(图e)。
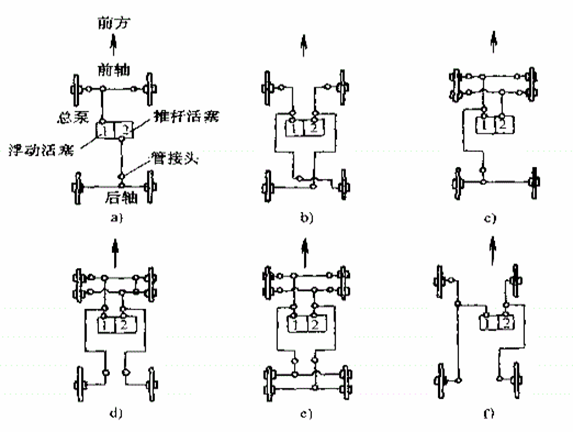
图2.2 制动器管路
下面分析这几种结构的优缺点,其中,II型和X型管道和布局简单,成本低,但是当II型的其中一个回路失效时,前轮就很容易抱死从而导致转向能力丧失,X型则会发生制动力不对称,使汽车丧失稳定性。HL、HH、LL型结构和管道布置都较为复杂,本次设计不予考虑。而HI型的回路失效时,能够使用单轴半环时,此时制动回路的制动力剩余较大,但应用此回路的汽车在紧急制动时,后轮易抱死。
综上所述并参考同类车型,本次设计选择X型布置方案,结构较为简单。
2.3第八代凯美瑞制动器设计技术参数
查阅相关资料可得如下表2.1:
表2.1 制动器设计基础参数
已知参数 | 第八代凯美瑞2019 2.0E |
整车质量(空载)(Kg) | 1530 |
整车质量(满载)(Kg) | 2000 |
轴距(mm) | 2825 |
质心高度(mm) | 600 |
前轴距(mm) | 1270 |
后轴距(mm) | 1555 |
最大扭矩(N/m) | 210 |
最高车速(Km/h) | 205 |
车轮 | 205/65 R16 |
2.4浮钳盘式制动器的主要参数选择及计算
2.4.1制动盘直径D
当选择制动盘的直径 D时,制动盘的直径D一般选择为轮毂直径的70%-79%,为了匹配车轮直径,它应该在一个合适的范围内。根据设计经验,当轿车的总质量超过2t时,制动盘的直径取该范围的上限。在保持有效制动性能的情况下,应尽可能使部件更小更轻。根据设计参数,轮辋直径Dr为16英寸(1英寸= 2.54cm),并且由于满载质量为2000kg,因此采用上限。在本设计中:D= 72%Dr = 79%x16x25.4mm= 321.056mm ,取D=320mm。
2.4.2制动盘厚度h
制动盘的厚度h是制动盘质量和运行期间温度升高的决定性因素。而本次设计中前轮为动力转向轮,因此前轮选取通风盘,后轮选取实心盘。通风制动盘选择两个制动面上的冷却叶片,增加制动盘铸件的冷却面积,加速散热。根据车型和一般设计准则,实心式制动盘的厚度为10毫米~20毫米,设置通风通道的制动盘厚度为20毫米~50毫米,。在本设计中,使用通风式盘式制动盘,h为25毫米,实心盘式制动盘为15毫米。
2.4.3摩擦衬块外半径R2与内半径R1
在制动器设计中,摩擦衬块的外半径R2的制动盘的外径相匹配,并且所述摩擦垫的内半径R1是关系到外半径。设计经验R2 / R1比应小于1.5。当该比率过大时,摩擦衬块的外圆周和内圆周的速度制动时有很大的不同,从而导致不均匀磨损和降低的摩擦接触面积,这最终导致大的波动在制动扭矩的范围内。在此设计中,根据制动盘的直径,外半径R2= 154mm,内半径R1=110mm. R2/R1=1.4lt;1.5,符合要求。,
2.4.4摩擦衬块工作面积A
摩擦衬块的单位面积是根据相关标准选取,基于所述车辆的质量,范围从1.6kg/cm2至3.5kg / cm 2的选择,一般。当车辆的空载质量1530kg,在无负载在前轮的负荷842.2kg。所以计算可知在本设计中且由上述计算以及参考其他同类车型取A=70cm2。
2.4.5 制动驱动机构对制动盘的压紧力F0
如上所述并且需要简单的结构,在车轮制动器中的方便布置等,制动器是液压驱动的活塞式机构,并且制动压力由以下关系确定。由制动缸施加到制动盘的压力F0与轮缸直径d和制动管路压力P之间的关系如下:
(2.1)
以上是毕业论文大纲或资料介绍,该课题完整毕业论文、开题报告、任务书、程序设计、图纸设计等资料请添加微信获取,微信号:bysjorg。
相关图片展示: